Chromic Acid Anodizing is a surface treatment process widely used in the aerospace industry to enhance the durability and performance of aluminum components. It involves the controlled oxidation of aluminum surfaces in a chromic acid solution, resulting in a protective oxide layer. All these anodizing processes offer distinct advantages and are suitable for certain materials than others.
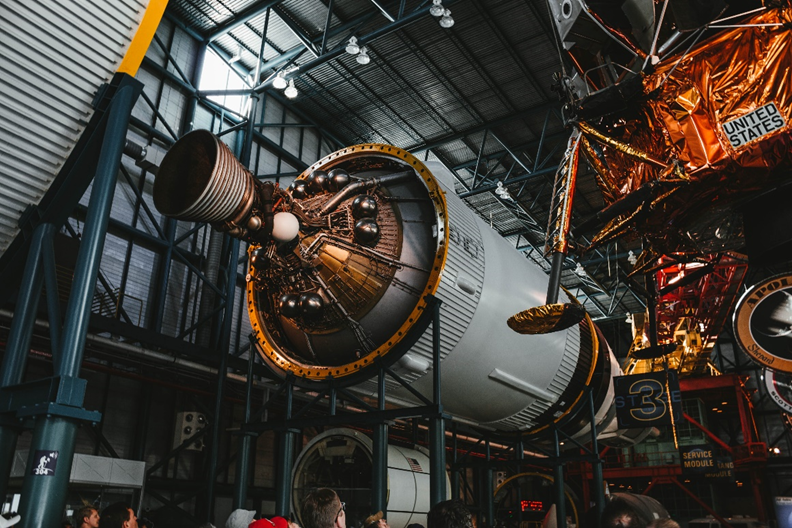
The aerospace industry, encompassing a diverse array of equipment such as aircraft, jet engines, satellites, and more, relies heavily on metal, plastic, and composite materials for its components. Aerospace anodizing is a pivotal step in the manufacturing of aluminum, titanium, and magnesium components, aimed at fortifying them against wear and tear. Four distinct types of anodizing – phosphoric acid, boric sulfuric acid, chromic acid, and sulfuric acid – are employed based on specific material requirements.
Importance of Surface Treatment in Aerospace Component Design
Surface treatment is critical in aerospace engineering to address challenges such as corrosion, wear, and adhesion. Chromic Acid Anodizing plays a pivotal role in achieving these objectives, ensuring the longevity and reliability of aerospace components.
- Corrosion Resistance
Chromic Acid Anodizing provides superior corrosion resistance by forming a protective oxide layer, crucial for aerospace components exposed to harsh environments.
- Wear Resistance
The hardened surface resulting from anodizing improves wear resistance, enhancing the lifespan of components subjected to mechanical stress.
- Dimensional Stability
Anodizing contributes to dimensional stability, a critical factor in aerospace applications where precise tolerances are essential.
- Enhanced Adhesion for Coatings
The anodized surface promotes better adhesion for subsequent coatings, facilitating the application of protective or decorative layers.
Over the years, we have served many aerospace engineering services to achieve their targeted goals through anodizing and electro polishing. We understand that, unlike other industries, these services have specific needs for custom tanks and metal finishing tanks. Thus, our experts and engineers work closely with them to meet these requirements. They can help incorporate these systems to your existing process line or create an entirely new line from scratch.
Steps Involved in Chromic Acid Anodizing
The aerospace anodizing process involves several key steps:
- Enhancing Aesthetic Appeal: Metal finishing involves processes such as sanding and polishing to enhance the visual appeal of surfaces.
- Surface Preparation and Cleaning: Various steps like precleaning, degreasing, alkaline cleaning, and deoxidizing are employed to remove markings, soils, grease, oil, and oxides, ensuring a clean surface for subsequent treatments.
- Anodization and Final Touch: The final stages include masking, alkaline etching/ desmutting, anodizing to form a protective coating, rinsing to eliminate trapped acid, and dyeing for color, followed by sealing to set the dye.
Chromic Acid Anodizing vs Sulfuric Acid Anodizing.
Chromic Acid Anodizing offers superior corrosion resistance and paint adhesion but is environmentally problematic. On the other hand, Sulfuric Acid Anodizing is more versatile, environmentally friendly, and cost-effective, although it may have some compromises in terms of coating thickness and certain material compatibility.
- Chromic Acid Anodizing:
- Advantages:
- Provides excellent corrosion resistance.
- Offers better paint adhesion.
- Creates a thin, dense anodic coating.
- Disadvantages:
- Considered environmentally hazardous due to the toxicity of chromic acid.
- Lower electrical efficiency in the anodizing process.
- Limited to specific alloys and applications.
- Advantages:
- Sulfuric Acid Anodizing:
- Advantages:
- Widely applicable to a broad range of alloys.
- More environmentally friendly compared to chromic acid.
- Higher electrical efficiency, making it a cost-effective option.
- Disadvantages:
- Anodic coatings may be less corrosion-resistant than those produced by chromic acid.
- Paint adhesion may not be as strong.
- Thicker coatings compared to chromic acid anodizing.
- Advantages:
Conclusion :
In conclusion, the role of chromic acid anodizing in aerospace component design is integral to ensuring the longevity, reliability, and safety of critical parts in the aerospace industry. The meticulous steps involved in the anodizing process, from metal finishing to dyeing, play a crucial role in enhancing the functionality and protection of components exposed to challenging environments. We has successfully served aerospace engineering services by providing tailored metal finishing systems for anodizing and electropolishing.
FAQ
- How Long Will Chromic Acid Anodizing Last?
A chromic acid-anodized surface should last at least 10–20 years, depending on the anodized layer’s thickness and porosity.
- What Are the Limitations of Chromic Acid Anodizing?
Touch-ups of damaged sections can be more visible compared to air-dry paint touch-ups of painted surfaces.
- Is Chromic Acid Prone to Rust ?
No, chromic acid-anodized materials are not prone to rust. Aluminum, in particular, does not rust, but it can oxidize or corrode. Chromic acid anodizing is performed to protect the metal against rust.